Since 2016, PLATIRUS project has researched, experimented and developed 11 innovative, cost-efficient and sustainable technologies to recover platinum group metals from spent autocataysts, mining and electronic waste. This has been achieved through the joint work of leading European researchers, academics, scientists and experts, and an ambitious work programme.
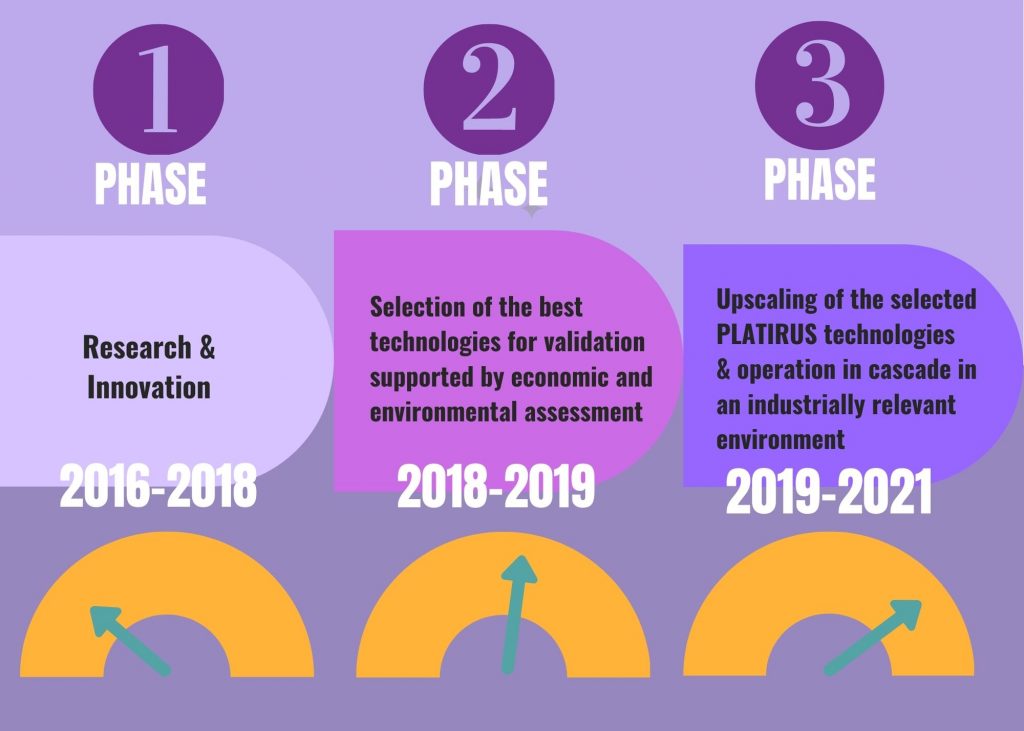
Each of the PLATIRUS partner VITO, SINTEF, TU Wein, TECNALIA and KU Leuven have researched and developed their respective technologies (see Figure 2) during the Research and Innovation (R&I) phase. Within the project scope of work, there are 3 main steps: leaching, separation and recovery (see Figure 3). All partners have collaborated on analytical methods to ensure consistency of the project results among them.
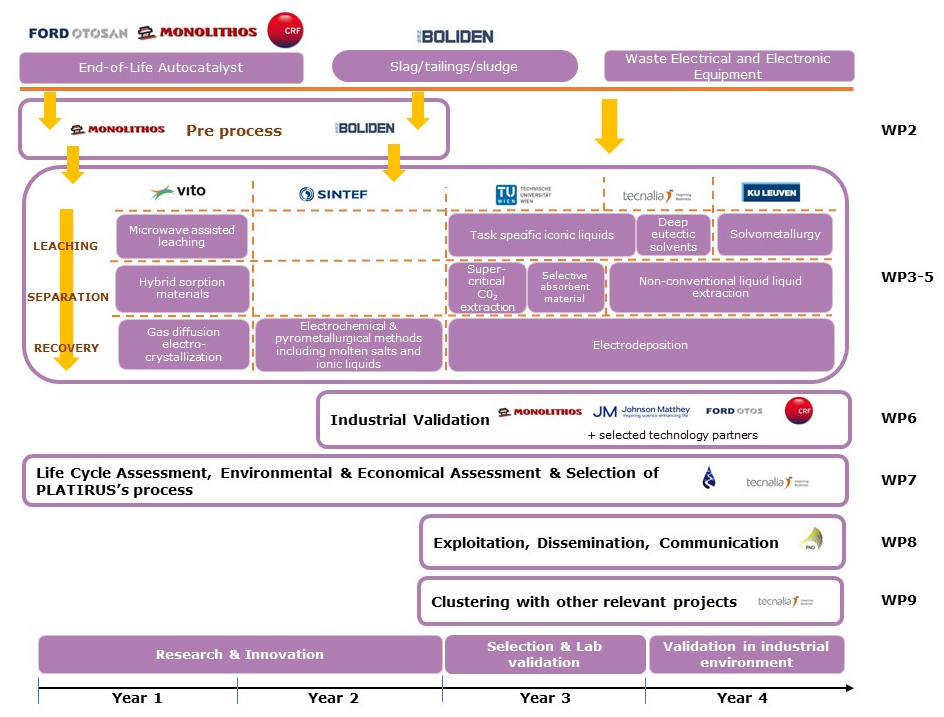
*As of April 2020 ENV-Aqua Solutions Ltd is not part of the project consortium
.
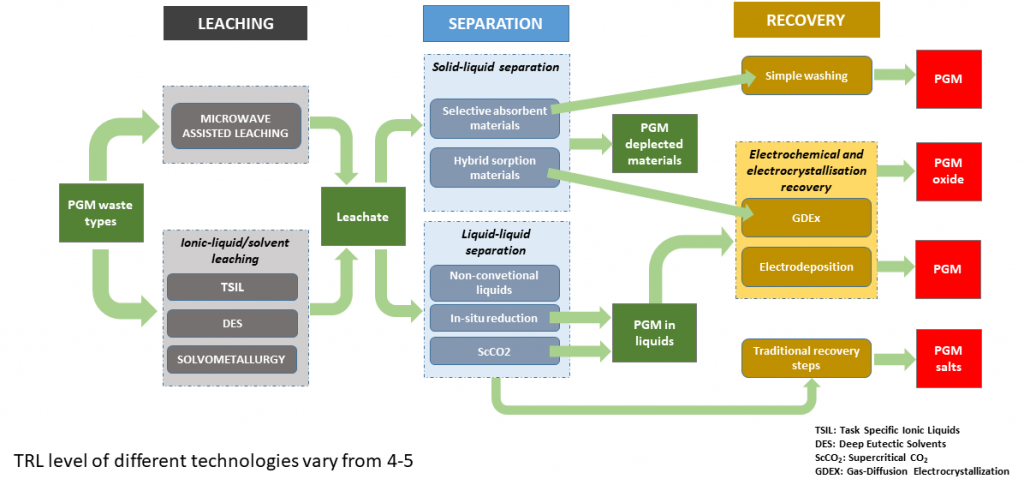
A standard sample with a known and certified concentration of each PGM (Pt, Pd and Rh) was used by each partner to evaluate different analytical methods to ensure accuracy and repeatable results. All key outcomes and experimental results are based on processing the same waste feedstock, namely milled spent autocatalyst feed containing palladium, platinum and rhodium. This feed comprises over 100 different de-canned and milled automotive catalysts from the open market. The grain size was <2 mm. The feed contained 1588 ± 18 ppm palladium, 912 ± 5 ppm platinum and 327 ± 9 ppm rhodium as characterised using X-ray fluorescence spectral analysis.
The below table (Table1) presents a summary of the technologies investigated in the PLATIRUS project and experimental results that have been achieved.
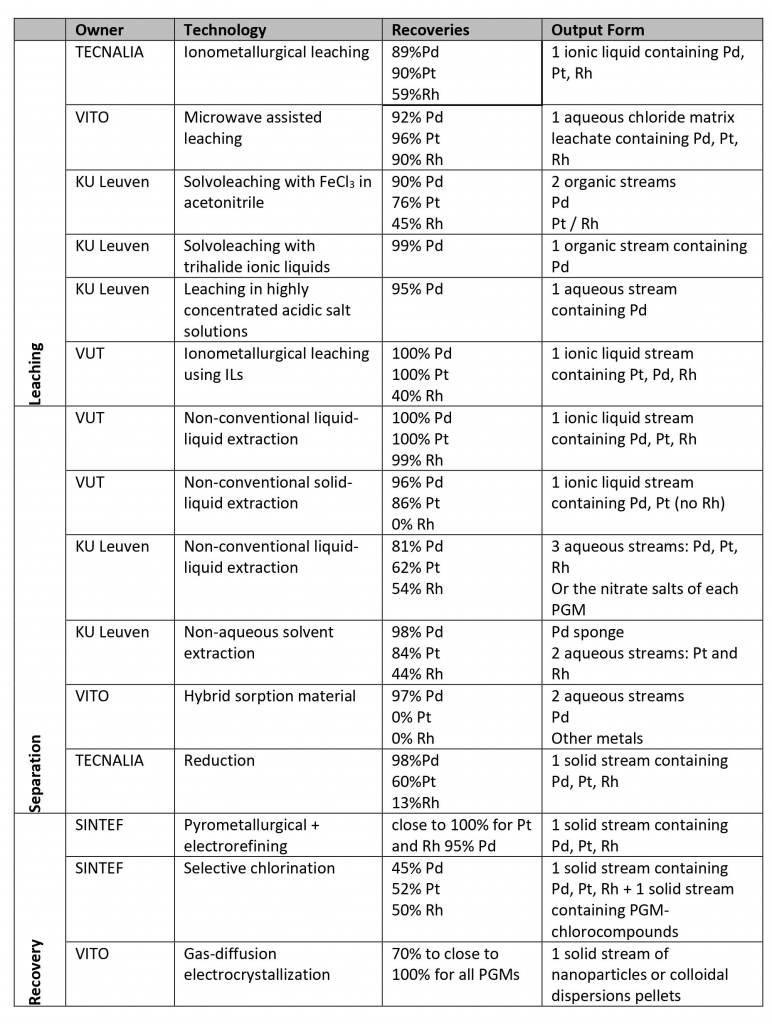
Selection criteria
All 11 technologies were evaluated against key performance indicators (KPIs): recovery, environmental impact and process compatibility. All different combinations of the PLATIRUS technologies and the baseline were evaluated. Figure 4 shows the evaluation results for the most relevant process combinations.
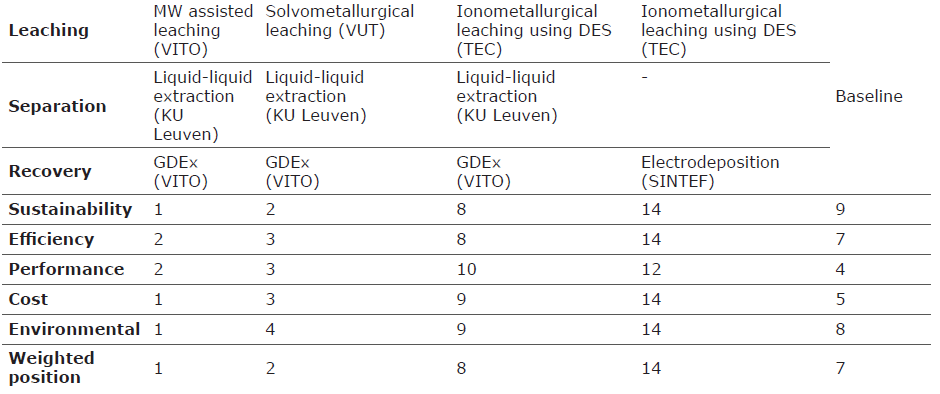
Selected technologies for market uptake
One technology per phase (leaching, separation, recovery) has been selected based on set of parameters such as selectivity, efficiency energy and environmental requirements. Three selected technologies demonstrated at VITO and KU Leuven sites have successfully achieve the highest score based on the project selection criteria. They have successfully recovered PGMs from secondary resources and demonstrated that it is possible to use those recycled PGMs to manufacture new automotive catalysts. The considered technologies are characterized by their efficiency, high selectivity, environmentally friendly concept, flexibility to recover other valuable metals and last but not least their low CAPEX and OPEX.
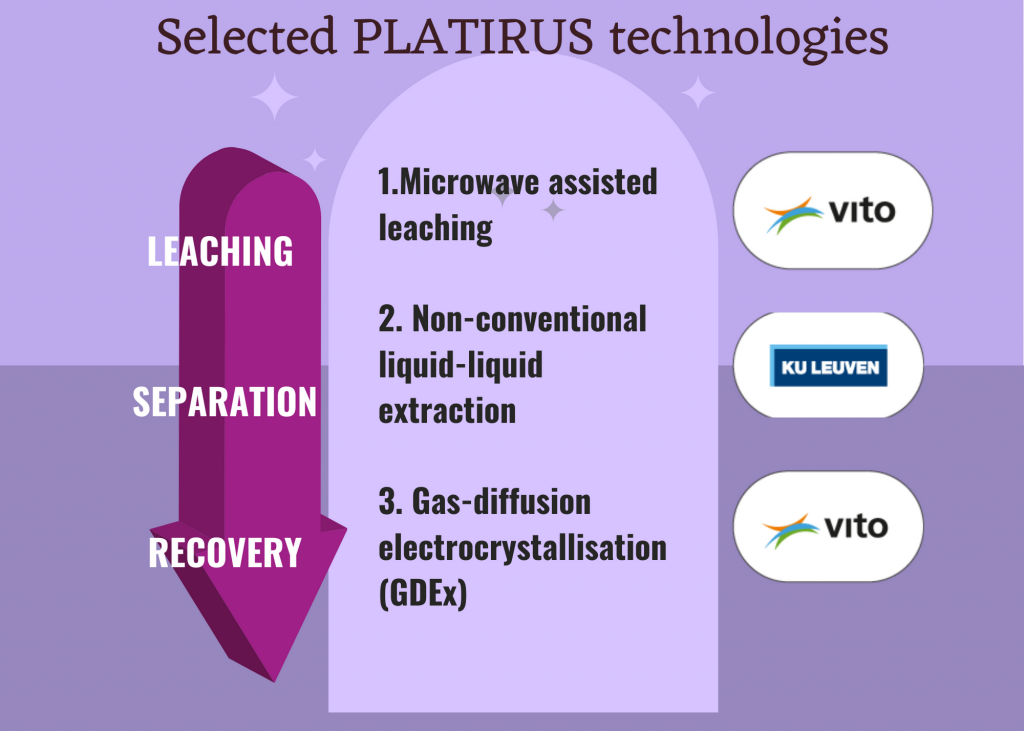
In addition to the 3 selected technologies, conventional chemical transformations were employed to convert the PLATIRUS outputs into the correct form for automotive catalysts’ production. The demonstration was carried out using technology and equipment appropriate, available and compatible to process the ~1.3 kg autocatalyst (~15 l pgm solution).
Over a six-month period, the PLATIRUS team successfully operated the PLATIRUS flowsheet in cascade and processed the feedstock producing 1.2 g palladium, 0.8 g platinum and 0.1 g rhodium in nitrate form with a purity of 92-99% (as a reference market palladium nitrate solution is sold with a purity of 99.98%).
The selected PLATIRUS process was tested in cascade on milled spent ceramic catalyst material and consists of:
- MW-assisted leaching: Overall ~1.35 kg material was leached in 6 M HCl
- Solvent extraction with ionic liquids: 12 L of leachate processed by a continuous solvent extraction demonstrator, using mixer-settlers
- Gas diffusion electrocrystallization: Recovered ~70% of Pd from the strip sample with a purity of 91-93%
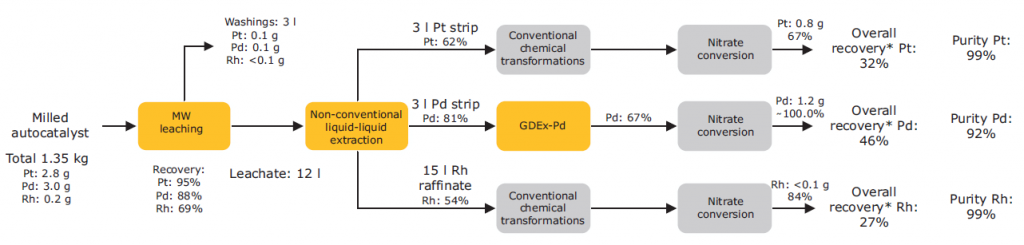
Each individual technology reached TRL 5, whereas the overall PLATIRUS flowsheet was tested at TRL 4. Further optimization and upscaling of all 3 processing steps is planned.
If you want to learn more about each of the technologies explored within PLATIRUS project, please check the detailed project overview recently published in Johnson Matthey Technology Review:
EU Innovation technologies & Patent
Six PLATIRUS technologies were awarded by the European Commission as Great EU innovations via the Innovation Radar Prize. The Innovation Radar prize is awarded to Europe’s most promising innovators and innovations emerging from the EU-funded research and innovation projects for 2020.
The PLATIRUS, project funded by the EU under the frame of Horizon 2020 programme, won the prize 6 times in different categories during 2018 and 2020 awarding ceremonies.
Six of the breakthrough PLATIRUS technologies are listed below:
- VITO – Advanced MW-assisted leaching of Platinum Group Metals (PGMs) from automotive catalyst materials.
- Technical University of Vienna – Improved ionic liquids based leaching and pre-concentration of platinum group materials from spent car catalysts.
- VITO – Platinum Group Metals (PGMs) recovery by Gas-Diffusion Electrocrystallization (GDEx). This breakthrough technology has been patented.
- SINTEF – Process for recovering Platinum Group Metals from material like ores, tailings and recyclates by selective chlorination and subsequent reduction into metals in a molten salt reaction media.
- KU Leuven – Process for separation of Platinum Group metals (PGMs) and gold (Au) by split-anion extraction with ionic liquids.
- VITO – Regenerable solid phase extraction (SPE) material to selectively separate Platinum Group Metals (PGMs) metals.
More information about each of the innovative technologies you can find here: https://www.innoradar.eu/resultbykeyword/PLATIRUS
*This article contains information (text and visual material) form the Johnson Matthey Technology Review 2021. All copyrights reserved to:
Johnson Matthey Technol. Rev., 2021, 65, (1), 127
doi:10.1595/205651321×16057842276133
The copyright holder is Johnson Matthey Plc.