During PLATIRUS project, VITO has used microwave heating to improve metal recovery from waste materials through increasing the selectively and efficiency of the leaching processes and decreasing the energy use.
VITO has developed a microwave assisted two-step platinum group metal (PGMs) extraction process for spent automotive ceramic catalysts. The method has proven to reduce energy consumption in comparison to traditionally heated reaction systems. During the first step, or so-called sulfation roasting step, the spent material catalysts is mixed with a sulphate salt and heated through microwave (MW) irradiation to high temperatures. This process transforms the present PGM to a soluble species that can be leached. Thus, the second step consists of leaching the roasted material. Optimal leaching occurred in a 1 M HCl solution when heated to 105 °C by microwaves.
The combination of the MW roasting and leaching allows for all PGMs present to be extracted with high yields (96% Pd, 85% Pt and >96% Rh). This is a remarkable achievement, as through the combination of both processes, the valuable PGMs were recovered at higher rates than those reported in literature for the individual processes. MW radiation was directly absorbed by the material that was to be roasted, leading to a fast heating and limited energy loss with respect to traditional heating in a furnace.
The published findings also provided an in-depth insight into the sulfation roasting mechanisms that occur for spent automotive ceramic catalysts and can lead to further improvements of PGM recoveries.
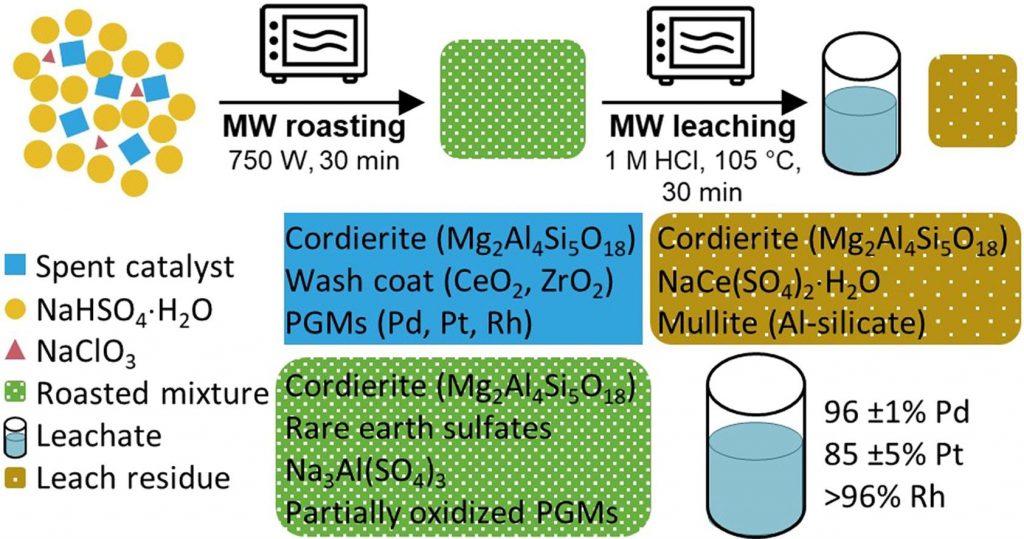
The development of this process and research that led to further insights in the roasting process has recently been published in Minerals Engineering and can be found here: https://doi.org/10.1016/j.mineng.2019.106153; or downloaded here: https://zenodo.org/record/3565950.